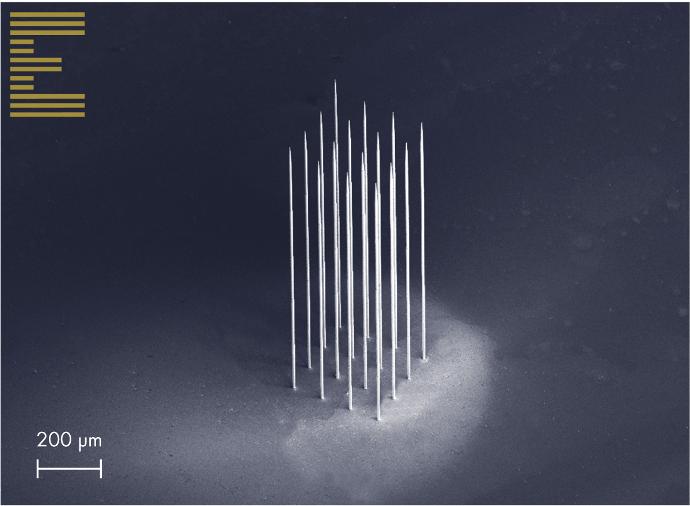
"Even in a benign AI scenario, we will be left behind"
No field of AI inspires both wonderment and fear of the future possibilities more than neuroprosthetics. For some people, talk of brain-computer interfaces (BCIs) may spark images of a post-apocalyptic future; one in which life has imitated art, and the portents of Sci-Fi films such as I-Robot have been disastrously realized.
However, speak with researchers at any company involved in BCIs/BMIs, and an altogether different reality emerges; one quite the opposite of the dystopian cyborg future so often predicted by Hollywood.
Defined simply as the coupling of neuroscience with biomedical engineering, neuroprosthetics involve the use of external computing power to either assist or replace human functionality. Whilst neural control of robotic limbs has existed since 2008, new approaches toward a human-AI integration have recently come into being.
Active Companies
For companies such as Musk's own Neuralink, the focus is firmly on altruistic use of science. Like Paradromics, Columbia University and others, Neuralink are devoting their energies to improving the lives of people suffering from hugely disempowering conditions such as Parkinson’s or Alzheimer’s, which are due to degradation of neural pathways. A far cry from computers taking over the human race, these BCI applications are using artificial computing systems and power to compensate for damaged nerve networks and brain functionalities in the patients.
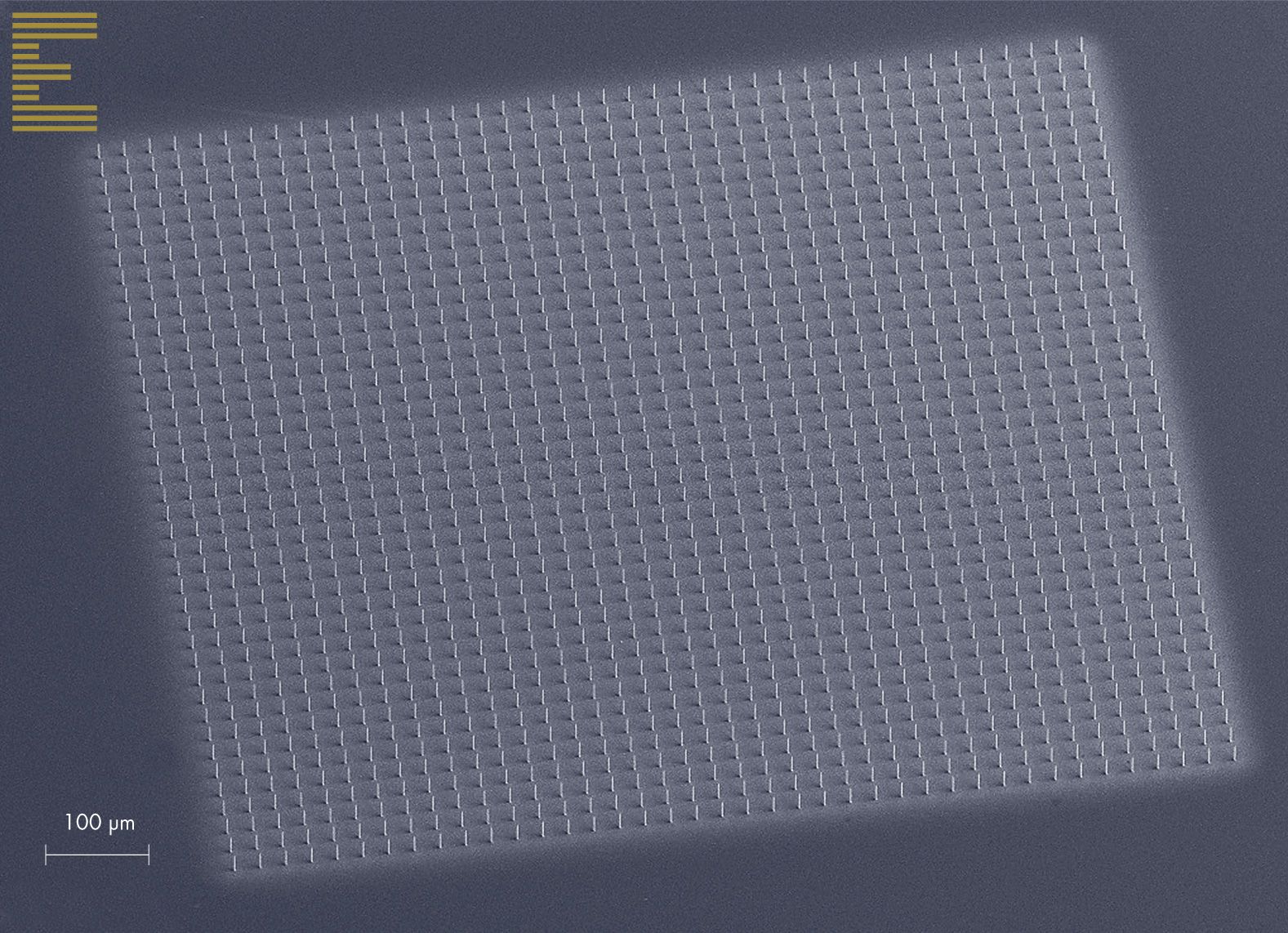
Applications
Through the placement of an electrode sensor on the brain, connected to external computing systems, these technologies are intended to perceive and perform functions which are no longer possible by the human body. From empowering aphasic individuals with the power of speech, such as at Columbia University’s Zuckerman Institute, through to seizure prevention in patients with drug-resistant epilepsy [1] these applications are truly game-changing.
The realities of having electrodes implanted into the brain is justifiably a concerning idea for some, but the possibilities which such devices open-up for patients cannot be overstated. Enabling a quadriplegic individual to walk again by means of a thought-controlled exoskeleton is the granting of a freedom in comprehensible to most able-bodied people. Similarly, giving back the power of speech to those with aphasia is an astonishing gift from an area of science still very much in its infancy. Some of the brightest minds on the planet are devoting themselves to advancing this novel and profound area of science, and what the future may hold is very exciting indeed.
Inherent Technical Difficulties
Of course, these modern-day miracles are not a plug-and-play solution. This is necessarily invasive technology which of course requires an implanted device –a highly complex task.
Generally termed electrocorticography (ECoG), these implanted devices, which lie directly on the brain surface, offer much higher fidelity information than externally located electrodes, but present much greater complexity in terms of attachment. Not least is the need for bio-compatible microscopic electrodes capable of conducting electrical signals from the brain, and which are tiny enough to be left in situ indefinitely. Defined as “µECoG”, the use of microscopic electrodes is a recent revolution which is fast gathering momentum.
Shortcomings of Existing Technology
Perhaps the main shortcoming of existing implantable technology is the “mechanical mismatch between conventional rigid electronic materials and the dynamic, soft, and curvilinear human body” [2].
The inflexible nature of typical substrates present genuine concerns of long-term comfort and durability. This is accompanied by the need for high fidelity signal conductivity by whatever materials are used, and in non-metals, this has presented problems.
Existing approaches predominantly offer gold or platinum electrodes, on a variety of substrate options, such as iridium, platinum, polyimide, gold, and others.
Use of flexible substrates containing arrays of micropillars have been explored as possible solutions, such as by Malliaras et al, [3] who constructed PEDOT:PSS microarrays containing electrodes covering an area of 10 × 10 µm2, with a center‐to‐center distance of 60 µm.
Since their study, PEDOT has been greatly investigated as a promising material in light of its combined attributes of conductivity and flexibility.
Possibilities with Exaddon's µAM Technology
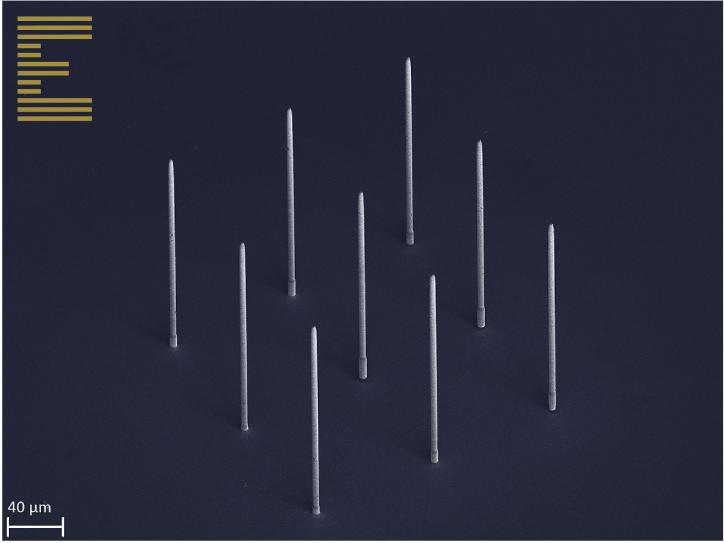
Exaddon’s unique µAM technology allows printing of micropillars in pure metal with high conductivity. With diameters below 1 µm possible, the CERES µAM print system is well-suited to printing the microscale metal structures necessary for conductive, mechanically stable electrodes. The submicrometer resolution of our system brings astonishing precision to the smallest metal manufacturing capability possible in 3D.
Shown is a microneedle array printed on PEDOT:PSS as a demonstration of a possible application of our CERES print technology to the emerging field of neuroprosthetics.
Reach out to us and learn more
Discuss your neural interface projects with us, and see how µAM can help
References
[1] https://www.ncbi.nlm.nih.gov/pmc/articles/PMC6914250/
[2] Mehrali M, Bagherifard S, Akbari M, et al. Blending Electronics with the Human Body: A Pathway toward a Cybernetic Future. Adv Sci (Weinh). 2018;5(10):1700931. Published 2018 Aug 1. doi:10.1002/advs.201700931
[3] Khodagholy D., Doublet T., Gurfinkel M., Quilichini P., Ismailova E., Leleux P., Herve T., Sanaur S., Bernard C., Malliaras G. G., Highly conformable conducting polymer electrodes for in vivo recordings. Adv. Mater. 2011, 23, H268.
Neuroprosthetics and Additive Micromanufacturing