Manufacturing Microcoils and Helices with µAM
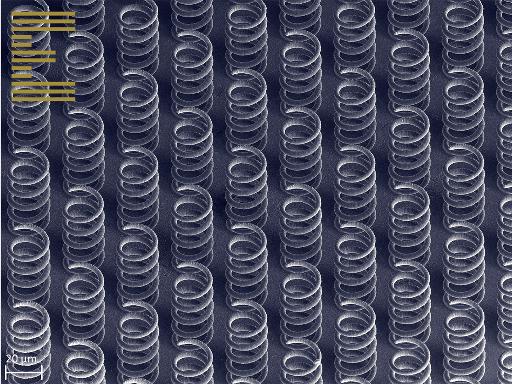
Each coil measures 20 micrometers in diameter.
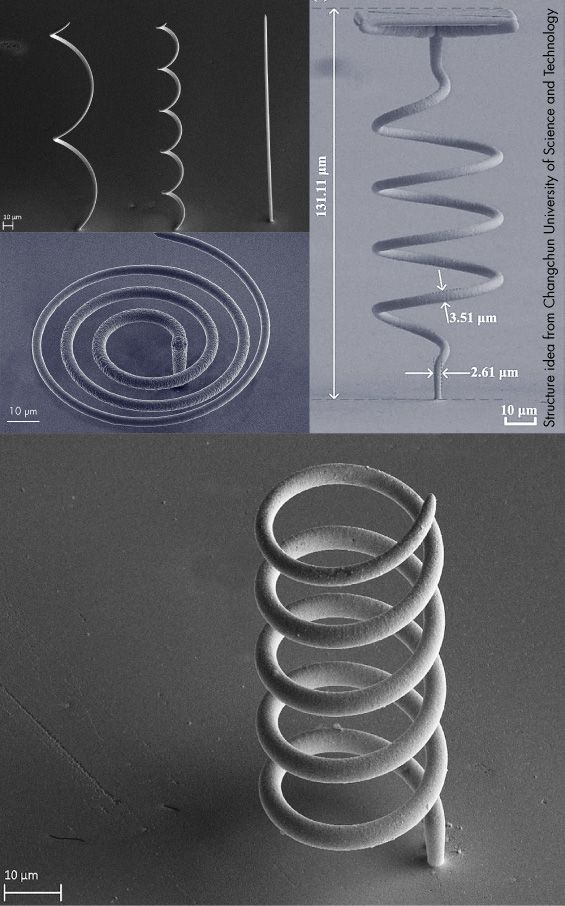
Manufacturing coils and helix structures with a diameter less than 300 micrometers is a complex challenge which is hardly addressed by conventional methods. Thanks to our additive micromanufacturing technology, coils down to 10 micrometers in diameter are possible using standard printing nozzles. Using custom nozzles, the diameter can go even smaller.
The CERES µAM print system can print coils in isolation or in array, with overall coil diameter, strand diameter, or pitch all able to be customized.
Advantages:
- Structures printed directly onto contact pads
- Wide range of designs possible
- Pure, high quality copper or gold (other metals possible)
- Excellent conductivity (~87% of bulk copper)
- Excellent adhesion to the substrate
-
More complicated designs feasible:
- Planar coils
- Intertwine multiple coils
- Strands can have different diameters
See the Publications page for our latest research in this area.
Use Cases of 3D Printed Microscale Metal Coils:
- Waveguides for THz applications
- Semiconductor contacting
- Electrode interfaces
- Photonics structures
- Cell transfection / membrane interaction
- Microscale materials properties investigation
- MEMS applications
Explore more microscale 3D Printing use cases: Fundamental Research
Open up new horizons in fundamental research with microscale 3D printing